HOWTO: Wie dokumentiert man Stillstände und Instandsetzung zur Verbesserung der OEE?
Um deine OEE zu verbessern, musst du wissen, welche Probleme in deinem Betrieb auftreten, die von der Zielbewertung ablenken. Wir werden uns damit beschäftigen, wie man die Stillstände und Verlust betrachtet, die sich auf die OEE auswirken. Wir stellen eine exemplarisches Muster/Vorlage vor, das die Grundlage für eine spätere Pareto-Analyse bildet.
Was ist OEE?
Hersteller auf der ganzen Welt streben jeden Tag danach, ihren geplanten Zeitplan einzuhalten, um ihre Produkte pünktlich und innerhalb des zugewiesenen Budgets/Preises herzustellen. Dies kann sehr kompliziert werden, da unerwartete Maschinenausfälle oder andere Faktoren wie Arbeitskräftemangel das fertige Produkt in Bezug auf Zeit und Geld beeinflussen können, was sie daran hindert, die maximale OEE zu erreichen.
Für Hersteller, die verstehen möchten, wo Verluste in ihrem Geschäft auftreten können und die Produktivität im Laufe der Zeit auf standardisierte Weise steigern möchten, ist die OEE eine Möglichkeit, dies zu verfolgen. Die Gesamteffektivität der Ausrüstung oder kurz OEE ist ein Maß für das Potenzial einer Maschine, das Möglichkeiten oder Bereiche von Bedenken aufzeigt, die verbessert werden können.
Die OEE wird in der Fertigungsindustrie eingesetzt, um Produktionsverluste zu identifizieren, zu überwachen und zu reduzieren. Als solche ist sie zu einem universellen Leistungskennwert (KPI) für Hersteller und eine bewährte Methode in der schlanken Produktion geworden. Deshalb sollten Maßnahmen ergriffen werden, um sie zu verbessern.
Die OEE ist sehr hilfreich für Prozesse, die von Maschinen gesteuert werden, wie automatisierte MES-gesteuerte Fertigungslinien. Produktionsprozesse mit großen manuellen Montageteilen werden oft mehr vom Arbeitstempo der Mitarbeiter als von der Taktung der Maschine beeinflusst.
Wie können wir die OEE in der Fertigungsindustrie umsetzen?
Ganz einfach, indem wir Ausfallzeiten, Wartungsarbeiten und Verluste dokumentieren, denn ohne diese Daten hast du keine Grundlage, um deinen Betrieb zu analysieren.
Warum sollten wir Ausfallzeiten oder Instandsetzungsarbeiten dokumentieren?
Du solltest deine Ausfallzeiten und Verluste dokumentieren, um herauszufinden, welche Probleme oder Schwierigkeiten regelmäßig auftreten und in welchen Abständen sie auftreten. Auf diese Weise können wir vorbeugende Wartung durchführen, bevor ein Problem auftritt, oder es in einem frühen Stadium angehen, sodass das kleine Problem, das du derzeit hast, nicht zu einem großen wird und du zusätzliche Ressourcen, sei es Zeit, Arbeitskraft, Material usw., benötigst.
Der Wert der Dokumentation ist sehr wichtig, denn ohne eine gute Dokumentation, die die Probleme zeigt, die eine Maschine hat, können wir nicht voraussagen:
- Was tritt auf?
- Wie oft tritt es auf?
- Welche Lösung wurde darauf angewendet?
- Was kann getan werden, um zu verhindern, dass es erneut auftritt?
- Oder was kann getan werden, um frühzeitig zu erfahren, dass das Problem aufgetreten ist?
Die OEE basiert auf drei Komponenten oder Faktoren: Verfügbarkeit, Leistung und Qualität. Verfügbarkeit: Verfügbarkeit umfasst alle Ereignisse, die die geplante Produktion lange genug gestoppt haben, um den Gesamtproduktionsplan zu beeinträchtigen, und sollte in der Dokumentation vermerkt werden (typischerweise können es mehrere Minuten sein). Leistung: Leistung umfasst alles, was bewirkt, dass der Herstellungsprozess mit weniger als maximaler Geschwindigkeit läuft (es umfasst sowohl langsame Zyklen als auch kleine Stopps). Qualität: Qualität umfasst alle hergestellten Teile, die nicht den Qualitätsstandards entsprechen und nachgearbeitet oder erneut hergestellt werden müssen.
Bedeutung der Stillstands-Dokumentation
Wenn du keine Dokumentation verwendest, verlässt du dich auf das Gedächtnis in Bezug auf die Hauptprobleme in der Produktion. Wenn du einen kleinen Betrieb mit wenigen Mitarbeitern hast, mag das ausreichen. Wenn du jedoch mehrere Schichten und größere Teams hast, ist es wichtig, Dinge schriftlich festzuhalten, um Wissen zu teilen und sich später zu erinnern.
Mit Dokumentation kannst du feststellen, welche Probleme wie häufig auftreten und deine Bemühungen zur Verbesserung der OEE priorisieren.
Methoden zur Verfolgung von Stillständen und Verlusten
Die Frage lautet also: "Wie dokumentieren wir Stillstände?"
Sie können auf zwei Arten verfolgt werden:
- Manuelle Dokumentation
- Automatische Dokumentation
Manuelle Dokumentation
Manuelle Dokumentation bedeutet, dass Stopps und Verluste von Hand durch das Team in einem Papier-Schichtbuch oder einem Software-Tool erfasst werden. Es gibt jedoch keine Automatisierung, um die Betreiber daran zu erinnern, die Dinge aufzuschreiben, sondern nur eine Vereinbarung, jede "Ausnahme" zu dokumentieren.
Diese Methode ist anfällig für menschliche Fehler, da es leicht ist, die Datenerfassung zu vergessen, und Ausfallzeiten werden oft nicht korrekt gemessen. Es besteht ein hohes Risiko für eine verzerrte Ansicht der tatsächlichen Produktionsleistung der Anlage.
- Nicht gemeldete Stillstände
- Tatsächliche Ausfallzeiten basieren auf "Schätzung"
Die Betreiber möchten sich möglicherweise nicht die Mühe machen, häufig auftretende Ausfallzeiten zu melden, wie z.B. Werkzeugwechsel. Selbst wenn Ausfallzeiten gemeldet werden, könnten wichtige Details in einem Bericht vergessen oder ausgelassen werden. Beschäftigte Betreiber könnten einfach dokumentieren, dass die Maschine aus war, ohne die genaue Dauer zu notieren.
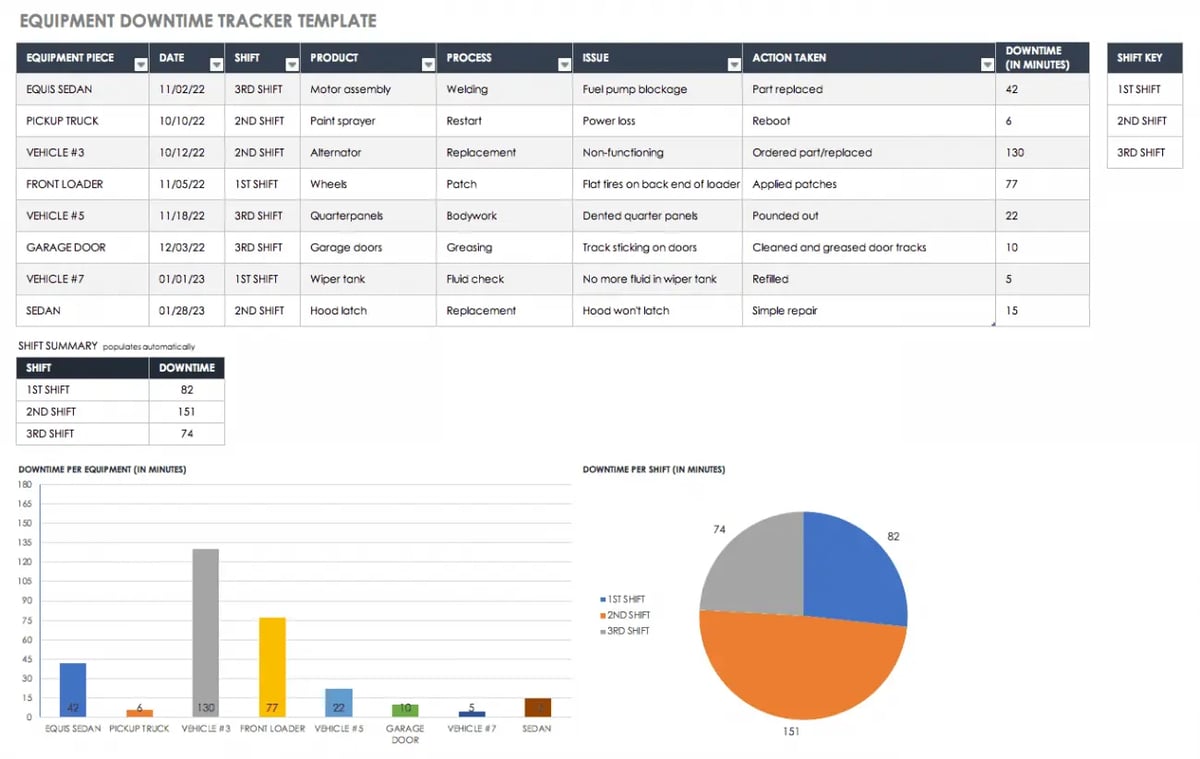
Beispiel für manuelle Dokumentation von Ausfallzeiten nach Eingabe in Excel-Tabelle von Smartsheet.
Allerdings ist die manuelle Dokumentation wesentlich kostengünstiger als die automatische Dokumentation und erfordert keine spezielle Ausrüstung.
Es ist ein guter Ausgangspunkt, um die Dokumentation zu starten, und die Daten können immer noch dazu verwendet werden, um Erkenntnisse zu gewinnen.
Automatische Maschinendokumentation
Die automatische Maschinendokumentation kann ein genaueres Bild davon vermitteln, was in deiner Fabrik vor sich geht. Durch die Dokumentation von Datenpunkten wie Ausrüstungsnutzung, Abschlussraten von Arbeitsaufträgen und Ausfallereignissen erhältst du ein klares Verständnis davon, wo deine Engpässe liegen und was getan werden muss, um sie zu beheben.
Normalerweise meldet ein Sensor oder der Maschinenstatus einen Stopp in der Linie elektronisch. Der Betreiber wird in der Regel auf einem Tablet, einem Computer oder einer HMI aufgefordert, den Stopp zu qualifizieren:
- Warum hat die Maschine gestoppt?
- Welche Maßnahmen wurden ergriffen?
- Häufig werden übliche Aufgaben kategorisiert ("Einrichtung", "wöchentliche Reinigung", ...)
Die Software erfasst die Dauer des Stopps und, wenn verfügbar, auch den Ausschuss zusammen mit den Notizen des Betreibers.
Die Automatisierung der Datenerfassung über die Maschinenüberwachung adressiert viele der Probleme, die bei manuellen Methoden auftreten.
Die Verwendung von Software, die mit dem Steuerungssystem der Maschine verknüpft ist, garantiert, dass genaue Start- und Stoppzeiten automatisch für alle Ausfallereignisse erfasst werden. Einige Systeme verhindern sogar, dass die Maschine neu gestartet wird, bis die Betreiber Gründe für die Ausfallzeit angeben, und die Auswahl der Gründe ist auf eine standardisierte Liste beschränkt, um genaue Informationen bereitzustellen. Auf diese Weise werden alle Stopps erfasst, unabhängig davon, ob sie nur wenige Minuten oder länger als eine Stunde dauern.
Normalerweise verwendete Systeme zur Verfolgung von Ausfallzeiten sind:
- Ein unternehmensweites integriertes Managementsystem (IMS)
- Fertigungsausführungssysteme (MES)
- Computerbasierte Instandhaltungsmanagementsysteme (CMMS / EAM)
- Spezielle Software zur Verfolgung von Ausfallzeiten, die mit dem PLC einer Maschine verbunden ist
- Maschinen-Datenlogger mit periodischen Datenübertragungen oder Telemetrie
Organisationen beschränken sich normalerweise nicht auf eine einzige Art der automatischen Dokumentation von Ausfallzeiten oder einer einzelnen Dokumentationssoftware. Die meisten der oben genannten Optionen können miteinander kombiniert werden, um bessere und genaue Daten über Stillstände zu liefern. Wie es so schön heißt: "Was gemessen wird, wird gemanaged." Die Berechnung von Ausfallzeiten mag einfach erscheinen, sollte jedoch durchgeführt werden. Daher sollten alle Stopps erfasst werden, unabhängig davon, ob sie ungeplant, geplant, kleine Stopps, langsame Zyklen, Produktabweichungen oder Startabweichungen sind.
Welche Art von Ausfallzeiten und Wartungsstopps gibt es?
Immer wenn ein Ausfall oder Wartungsstopp auftritt, sollte ein Kommentar im Zusammenhang mit der Dokumentation des Stopps hinzugefügt werden, in dem erklärt wird, um welchen Typ es sich handelte und welche Maßnahmen ergriffen wurden (sei es Arbeitskraft, Ersatzteil usw.), um das aufgetretene Problem zu lösen.
Diese Informationen sind sehr wertvoll, da der Text eine kurze Zusammenfassung dessen bietet, welche Art von Ausfallzeit auftrat, deren Ursachen und die durchgeführte Wartungsarbeit. Diese können später zur Verbesserung der OEE studiert werden. Normalerweise fallen diese Ausfälle/Stopps, mit denen eine Maschine konfrontiert ist, in diese Kategorien:
Das ist sehr wertvolle Information, da der Text eine kurze Zusammenfassung darüber liefert, welche Art von Ausfall auftrat, seine Ursachen und die durchgeführten Wartungsarbeiten. Diese können später zur Verbesserung der Gesamteffektivität der Anlagen (OEE) untersucht werden. In der Regel fallen die Probleme, mit denen eine Maschine konfrontiert ist, in diese Kategorien.
Geplante Stillstände sind Zeiten, in denen die Ausrüstung für die Produktion oder den Betrieb geplant ist, aber aufgrund eines geplanten Ereignisses nicht läuft. Beispiele hierfür sind Umrüstungen, Werkzeuganpassungen, Reinigung, geplante Wartungsarbeiten und Qualitätskontrollen. Einige Unternehmen kategorisieren auch Pausen und Besprechungen als geplante Stillstände.
Ungeplante Stillstände sind Ausfallzeiten, in denen die Ausrüstung für die Produktion geplant ist, aber aufgrund eines ungeplanten Ereignisses nicht läuft. Beispiele hierfür sind Ausrüstungsausfälle, Werkzeugfehler, ungeplante Wartungsarbeiten, Mangel an Arbeitskräften/Bedienern, Mangel an Material, Versorgungsmangel durch vorgelagerte Ausrüstung oder Blockade durch nachgelagerte Ausrüstung.
"Microstops" treten an automatisch überwachten Linien auf. Es gibt Tausende von kleinen Microstops, bei denen die Maschine auf ein vorgelagertes Verfahren wartet, um die Werkstücke weiterzuleiten. Die Linie ist nicht angehalten, sondern die Zufuhr wartet nur für einige Sekunden oder Millisekunden. Es ist nicht praktikabel, jeden Millisekunden-Stopp mit einem Kommentar zu versehen, aber die Summe dieser Microstops kann signifikant sein und sollte als Gesamtzeit gemessen werden. Diese Daten können im Zusammenhang mit "Langsame Zykluszeiten" kombiniert werden.
Langsame Zykluszeiten treten auf, wenn die Ausrüstung langsamer läuft als die ideale Zykluszeit (die theoretisch schnellstmögliche Zeit zur Herstellung eines einzelnen Teils). Beispiele hierfür sind verschmutzte oder abgenutzte Ausrüstung, mangelnde Schmierung, minderwertige Materialien, schlechte Umgebungsbedingungen, mangelnde Bedienererfahrung, Hochfahren und Herunterfahren. Dies kann mit "Microstops" in Verbindung stehen, da das Ergebnis auch eine geringere Durchsatzrate ist.
Ausschuss in der Produktion sind fehlerhafte Teile, die während des stabilen Produktionsprozesses hergestellt werden. Dies umfasst Teile, die nachgearbeitet werden können, da die OEE die Qualität aus der Perspektive der First Pass Yield misst. Beispiele hierfür sind falsche Maschineneinstellungen, Bedienungsfehler oder Handhabungsfehler, oder das Ablaufdatum (z.B. in der Pharmaindustrie).
Ausschuss nach dem Hochfahren sind fehlerhafte Teile, die während des Hochfahrens bis zum Erreichen einer stabilen Produktion hergestellt werden. Sie können nach jedem Anlagenhochfahren auftreten, werden jedoch am häufigsten nach Umrüstungen erfasst. Beispiele hierfür sind suboptimale Umrüstungen, Ausrüstung, die "Aufwärmzyklen" benötigt, oder Ausrüstung, die nach dem Hochfahren zwangsläufig Abfall erzeugt (z.B. eine Rollenpresse).
Wer sollte einen Stillstand dokumentieren?
Die erste Person, die im Falle eines Stillstands anwesend sein sollte, ist in der Regel der Bediener. Der Bediener ist gut geeignet, um diese Einträge vorzunehmen, da er/sie eng mit der Maschine vertraut ist und ihre Funktionsweise kennt.
Wenn der Instandhaltungsingenieur bei der Fehlersuche involviert ist, sollte er/sie auch seine/ihre Arbeit dokumentieren. Idealerweise ist die Instandhaltungsarbeit mit dem ursprünglichen Ereignis verknüpft und wird vom Bediener dokumentiert.
Was sollte dokumentiert werden?
Wir haben dies in den vorherigen Kapiteln besprochen, aber um zusammenzufassen.
Für jedes Ereignis (Stillstand/Verlust) solltest du:
- Einfache Klassifizierung wie oben erwähnt (ungeplant, geplant, Umrüstung, Pause...).
- Freitextkommentare (können 2 Felder für Bediener und Instandhaltungsingenieur sein).
- Menge des Verlusts (wenn nicht automatisch erfasst).
Das Hinzufügen von Kommentaren zur Dokumentation ist sehr wichtig, da es helfen kann, weitere Informationen über alle angewendeten Maßnahmen zur Problemlösung, deren Ursache und die angewendete Lösung zu erläutern.
Du kannst die Dokumentationsprotokolle im Detail lesen, herausfinden, welche Probleme am häufigsten auftreten. Du kannst auch Textanalyse-Software verwenden um das Durchlesen zu beschleunigen und automatisch häufige Probleme in den Texten zu finden.
Was ist der Prozess für Stillständserfassung?
Ein Problem tritt auf (z.B. ein Stillstand).
- Der Bediener arbeitet an dem Problem.
- Der Bediener dokumentiert seine Arbeit auf einem Tablet/HMI.
- Wenn das Problem gelöst ist, wird der Stillstand bestätigt und die Produktion wird wieder aufgenommen.
- Wenn das Problem nicht gelöst ist, wird die Instandhaltung gerufen.
- Die Instandhaltung versucht, das Problem zu beheben und dokumentiert ebenfalls ihre Arbeit im gleichen Log-Eintrag.
- Der Stillstand wird bestätigt, sobald die Maschine wieder startet.
Ein solcher Prozess erstellt einen Datensatz für jedes Ereignis, und die Arbeit des Bedieners und der Instandhaltung wird im gleichen Datensatz erfasst. Wenn der Stillstand automatisch erfasst wird, erhältst du auch Informationen über die Dauer.
Was nicht tun
Jedes Ereignis in einer eigenen Zeile in Excel erfassen. Einige Unternehmen führen Schichtbücher und erstellen pro Schicht einen Sammeleintrag. Wenn du mehrere Ereignisse in einem Datensatz miteinander vermischen, ist es für die spätere Analyse-Software schwer zu erkennen, welche Maßnahmen für welches Ereignis ergriffen wurden.
Das separate Erfassen jedes Ereignisses macht es auch für dich als Leser klarer, was zusammengehört.
Pareto-Analyse
Eine der besten Möglichkeiten, um Hauptprobleme zu identifizieren, besteht darin, Pareto-Diagramme zu erstellen, indem die Daten in einem Stillstandsprotokoll zusammengeführt werden.
Die Pareto-Analyse wird verwendet, um Probleme innerhalb einer Organisation zu identifizieren. Da oft ein überwältigender Anteil der Auswirkungen auf einen vergleichsweise kleinen Teil eines Unternehmens entfällt, strebt die Pareto-Analyse danach, die wesentlichen Probleme zu identifizieren, die es wert sind, gelöst zu werden, oder die erfolgreichen Aspekte eines Unternehmens.
Lese unseren Artikel über die Erstellung von Pareto-Diagrammen aus Wartungsprotokollen.
Es gibt auch ein Excel-Add-In, das dir bei der Erstellung von Pareto-Diagrammen aus Ihrer Stillstandsdokumentation helfen kann.
Learn über Prozesse, Rollen, Aufgaben, um aus Analyse Massnahmen zu machen.