HOWTO: Wie weiter mit Pareto Charts - Analyse Frameworks
Wir lernen, wie man Pareto-Diagramme betrachtet und welche Rahmenregelungen zur Erhöhung der Anlagenverfügbarkeit angewendet werden können. Wir berücksichtigen auch Reparaturkosten und Produktionsverluste, die durch Stillstände verursacht werden. Wir sind in der Lage, aus verschiedenen Blickwinkeln wirkungsvollere Entscheidungen über die Gesamtanlageneffektivität (OEE) des Unternehmens zu treffen.
Einleitung
Im Artikel "Erstellung von Pareto-Diagrammen aus Wartungsdokumentation" haben wir erklärt, was ein Pareto-Diagramm ist und wie du es verwenden kannst, um die wichtigsten Probleme in Bezug auf die Assets in unserem Produktions- oder Fertigungssystem effektiv zu visualisieren. Nun, da wir Daten klassifiziert und Pareto-Diagramme erstellt haben, was kommt als Nächstes? Dieser Artikel wird erläutern, wie du die Informationen analysieren kannst und was damit getan werden kann. Es ist wichtig zu verstehen, dass es bei der Analyse und Herangehensweise keine festen Regeln gibt, da Verfahren und Techniken je nach betrieblichem Kontext variieren können. Das wird uns jedoch nicht daran hindern, gemeinsam an einer Lösung zu arbeiten, die Ideen zur Bewältigung der spezifischen Herausforderungen des von dir untersuchten Produktionssystems liefert.
Eine gründliche Pareto-Analyse kann einen Unterschied in der Gesamteffizienz der Betriebsmittel (Overall Equipment Efficiency, OEE) eines Unternehmens bewirken, indem du die Hauptprobleme identifizierst, die sich signifikant auf ungeplante Ausfallzeiten, Leistung und Qualitätskomponenten auswirken.
OEE ist eine Metrik, die Verfügbarkeit, Qualität und Gesamtleistung in einem Unternehmen umfasst.
Wobei jeder der Faktoren durch die folgenden Gleichungen gegeben ist:
Wie wir sehen können, können wir, indem wir die Elemente identifizieren, die den größten Einfluss auf jeden der vorherigen Faktoren haben, die OEE des Unternehmens effektiv verbessern.
Analyse der klassifizierten Daten
Um die Verfügbarkeit unseres Unternehmens zu erhöhen, müssen wir zunächst die ungeplanten Ausfallzeiten bewerten. Die Verbesserung der Verfügbarkeit ist in industriellen Prozessen in der Regel eine der größten Herausforderungen aufgrund der Beteiligung mehrerer Faktoren, einschließlich Sicherheits- und Umweltfragen. Wie können wir Pareto-Diagramme nutzen, um genaue Analysen durchzuführen, die es uns ermöglichen, effektive Entscheidungen zu treffen und die Risiken von Unfällen, Umweltschäden oder ungeplanten Stilllegungen von Anlagen zu minimieren?
Schauen wir uns einige Analysen an:
Datenklassifikation: Ausfallzeit vs. Asset
Dies ist das erste Pareto-Diagramm, das wir analysieren müssen. Es liefert eine direkte Antwort auf unser Verfügbarkeitsproblem, indem du die Ausrüstung und/oder Systeme identifizierst, die die höchsten Ausfallzeiten aufweisen.
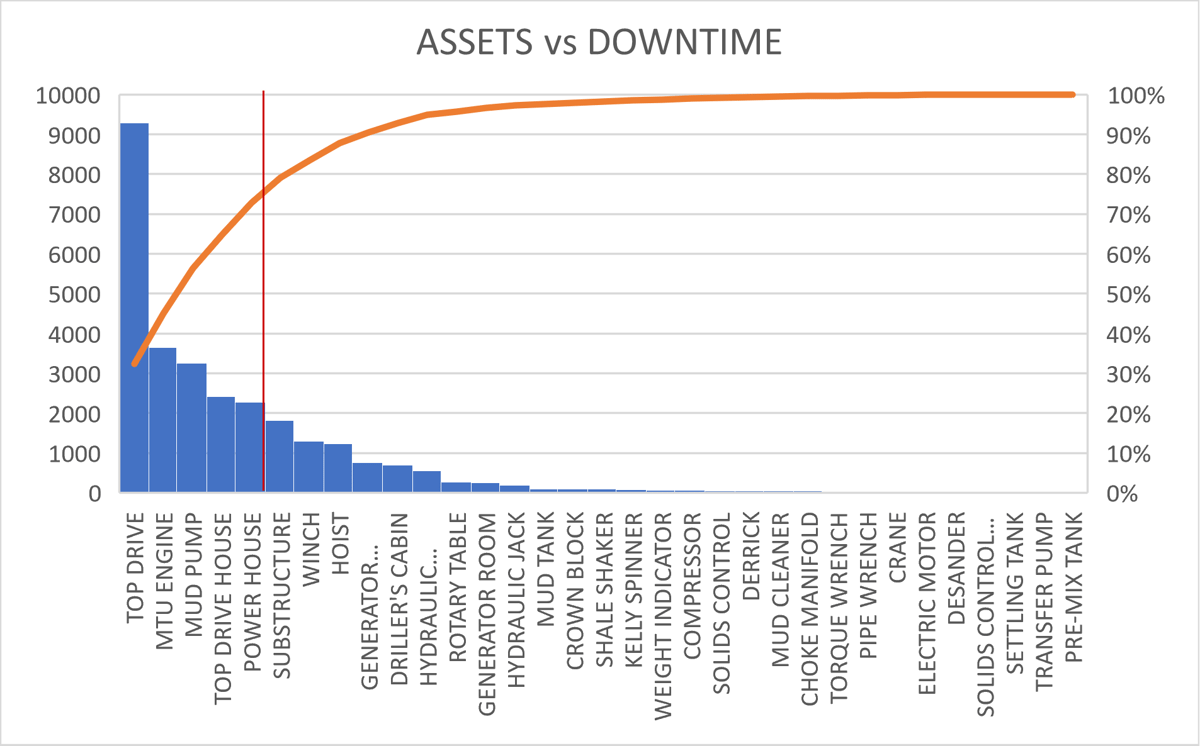
Abbildung 1: Ausfallzeit nach Asset
Die Grafik zeigt deutlich die Konzentration der Ausfallzeiten in der Top-Drive-Ausrüstung und zeigt, dass 80% der untersuchten Ausfallzeiten des Systems auf nur sechs Assets konzentriert sind.
Diese Daten sind schockierend und deuten darauf hin, dass sich die Verfügbarkeit um mehr als 30% steigern könnte, wenn du dich auf die Ausrüstung konzentrierst, die die meisten Ausfallzeiten verursacht.
Datenklassifikation: Ausfälle vs. Assets
Diese Analyse beantwortet eine entscheidende Frage in Produktionssystemen: Welche Ausrüstung und/oder Systeme haben die höchste Ausfallrate, oder anders ausgedrückt, wo konzentrieren sich die meisten Ausfälle im Produktionssystem, das wir untersuchen?
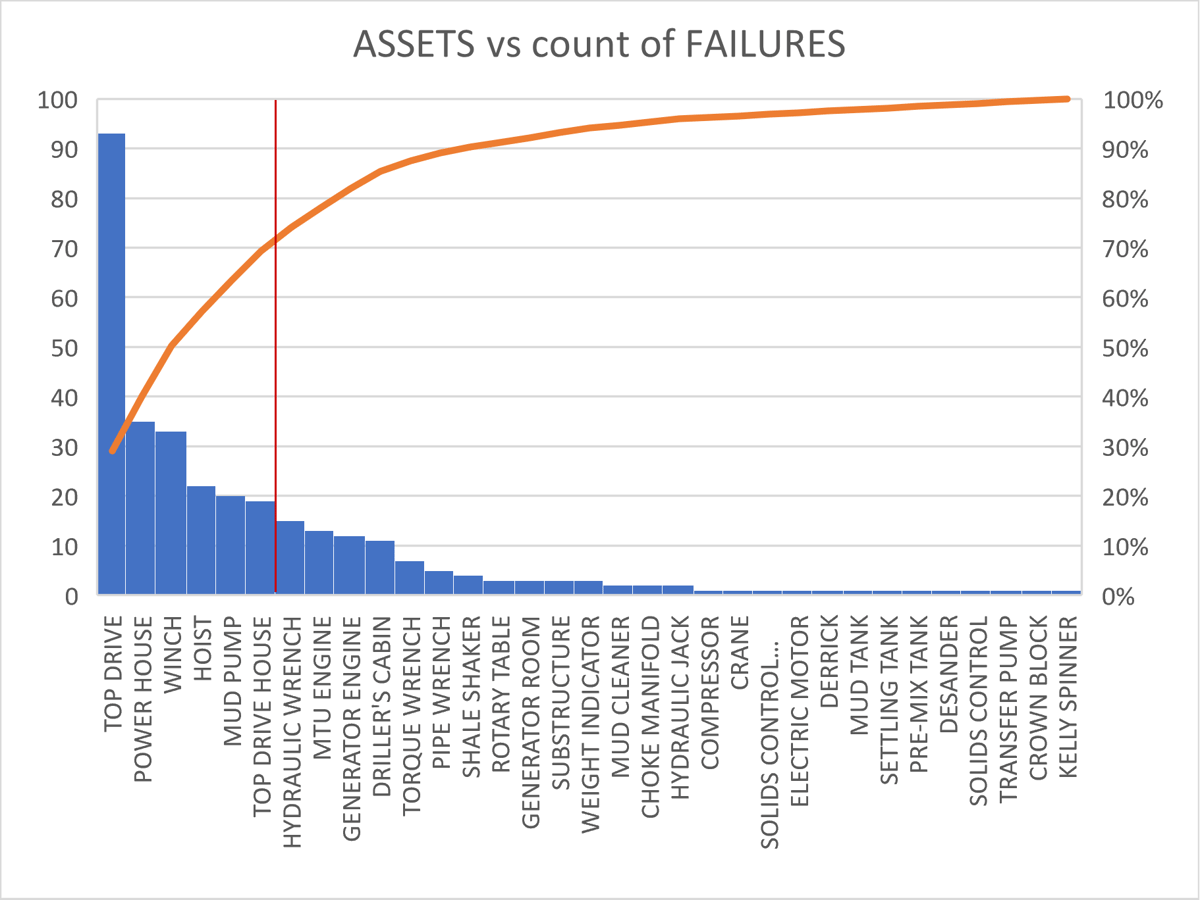
Abbildung 2: Ausfälle nach Asset
Im vorherigen Beispiel ist offensichtlich, dass jede Aktivität mit der TopDrive-Ausrüstung beginnen muss. Diese Ausrüstung allein macht etwa 30% aller Ausfälle aus. Wenn du dann das Diagramm betrachtest, das den kumulativen Prozentsatz der Ausfälle darstellt, wird deutlich, dass 80% der Ausfälle auf nur 8 Assets konzentriert sind. Daher wird die Implementierung eines umfassenden Ausfallreaktionsplans speziell für diese Ausrüstungen einen erheblichen Einfluss auf die Gesamtverfügbarkeit haben. Die Effizienz des Systems und damit die Gesamteffektivität der Betriebsmittel (OEE) unseres Produktionssystems.
Es ist möglich, unsere Ausfälle nicht nur nach Ausrüstung, sondern auch nach System oder einer anderen Eigenschaft zu charakterisieren. Zum Beispiel gibt es in einer Ölbohranlage fünf Hauptsysteme. Nach dem Beispiel der Studie haben sie die folgende Konzentration von Ausfällen.
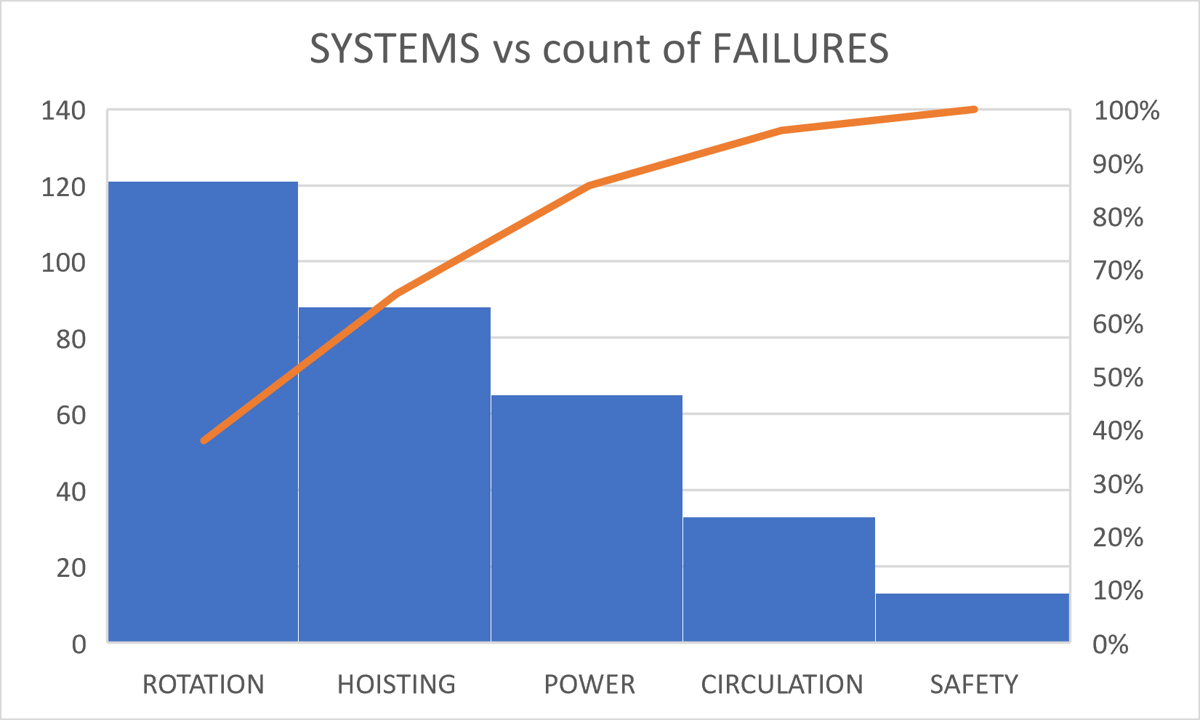
Abbildung 3: Ausfälle nach Systemen
Es ist interessant festzustellen, dass einige dieser Eigenschaften möglicherweise nicht explizit in der von den Arbeitern ausgefüllten Tabelle erwähnt werden, sondern in den abschließenden Kommentaren zur Beschreibung des Ausfalls und wie er behoben wurde. Dieses Feedback, in Kombination mit der Verwendung von TextAI-basierten Tools, kann verschiedene Ebenen dieser Fehler kategorisieren und uns in die Lage versetzen, umfassendere und spezifischere Eigenschaften zur Verbesserung unserer Analyse zu sammeln.
Es ist zu erkennen, dass das Rotationssystem den höchsten Anteil der Ausfälle aufweist. Wenn du die Teams im Rotationssystem betrachtest, die zur Gesamtzahl der Ausfälle beitragen, und ein Pareto-Diagramm verwendest, erhältst du das folgende Diagramm:
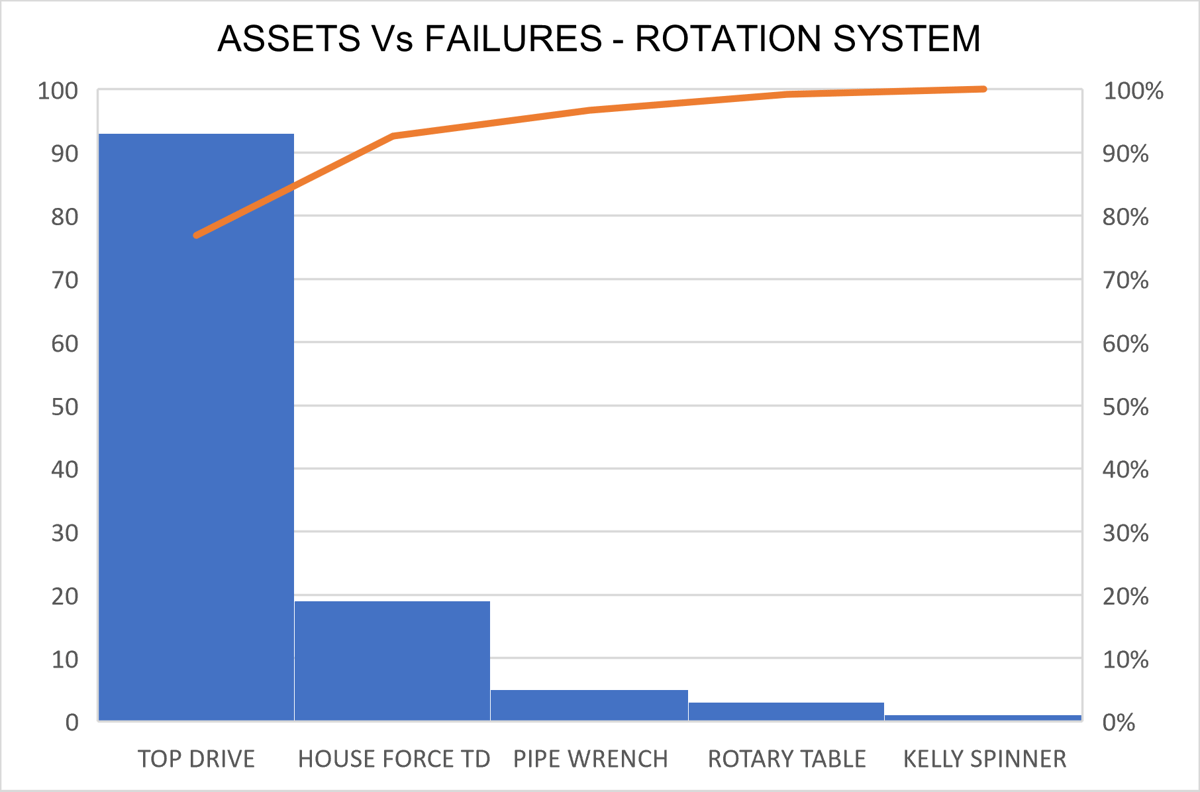
Abbildung 4: Ausfälle nach Asset – Rotationssystem
Dabei macht die TopDrive-Ausrüstung allein fast 80% der Gesamtzahl der Ausfälle aus.
Wir können feststellen, dass wir selbst bei der Anwendung von zwei unterschiedlichen Analysemethoden zu demselben Schluss kommen. Diese Konvergenz schmälert nicht die Glaubwürdigkeit eines der Ansätze, sondern steigert die Vollständigkeit unserer Studie.
Zusammenführen von klassifizierten Informationen für eine eingehende Analyse
Zusätzlich zu den vorherigen Grafiken, die die Anzahl der Ausfälle und Ausfallzeiten als erste Beobachtungen darstellen, können wir Muster, Trends und Beziehungen zwischen den verschiedenen Faktoren analysieren, die sich auf unseren Betrieb auswirken. Dadurch können wir unseren Entscheidungsprozess verbessern. Wir beziehen uns auf diese Analysen als Multifaktor-Analysen, und Pareto-Diagramme sind ein wichtiges Werkzeug, das uns dabei hilft, erfolgreiche Entscheidungen zu treffen.
Wir werden einige Beispiele bereitstellen, die uns helfen, das vorherige Konzept besser zu visualisieren. Die Informationen, die vom für die Behebung des Fehlers verantwortlichen Mitarbeiter erfasst wurden, umfassen verschiedene Felder wie Ausrüstung, System, Art des Fehlers (mechanisch, elektrisch, pneumatisch, Software, menschlich, Energie usw.), Ausfallzeit und Beobachtungen. Diese Felder hängen immer vom betrieblichen Kontext ab, und es können nie zu viele von ihnen sein. Wir dürfen nicht vergessen, dass die Hauptaufgabe der Person, die den Fehler behebt, darin besteht, ihn zu beheben. Komplexe Tabellen führen oft zu fehlerhaften Dateneingaben, was zu einem erheblichen Problem werden kann. Jetzt löst jeder Fehler einen Serviceauftrag aus, der zusätzliche Felder und Tabellen in verschiedenen Abteilungen des Unternehmens generiert. Ein Beispiel hierfür sind die bei der Reparatur verwendeten Materialien und die damit verbundenen Kosten, die zur Kennzahl "Reparaturkosten" beitragen.
Es gibt eine weitere Kennzahl namens "Verlust der Produktion", die das Ausmaß der Ausfallzeiten in Bezug auf die nicht produzierten Produkte misst. Dieser Indikator ist bedeutsam, da er Entscheidungsträgern ermöglicht, die Ausrüstungsausfälle und Ausfallzeiten zu visualisieren, die die meisten Produktionsverluste verursachen, was sich unmittelbar in finanziellen Verlusten niederschlägt. Dies gilt zum Beispiel, wenn du zwei identische Produktionslinien hast, die unterschiedliche Produkte herstellen, und eines davon einen deutlich höheren Marktwert als das andere hat. In diesem Fall führt ein Ausfall in der Produktionslinie zu derselben Ausfallzeit und Reparaturkosten, führt jedoch zu erheblichen wirtschaftlichen Verlusten aufgrund des Produktionsausfalls. In dem Beispiel mit den Bohrern, an dem wir im vorherigen Kapitel gearbeitet haben, könnte es sich um ein Ölfeld handeln, das erheblich mehr Öl produziert als ein anderes. Ein Ausfall in einem der Bohrer führt daher zu einem erheblichen Rückgang der Produktion. Ein weiteres Beispiel könnte ein Pharmaunternehmen sein, das zwei identische Produktionslinien betreibt. Eine Linie ist jedoch auf die Herstellung von Vitaminen spezialisiert, während die andere auf die Herstellung eines Arzneimittels mit erheblichen sozialen und wirtschaftlichen Auswirkungen wie Insulin ausgerichtet ist.
Ein Pareto-Diagramm, das die bedeutendsten Auswirkungen auf verschiedene Faktoren identifiziert, liefert uns ein präziseres Verständnis und eine gründliche Analyse der Realität unseres Produktionssystems. Daher können wir wirksamere Aktionspläne entwickeln, die einen größeren Einfluss auf die Gesamteffektivität der Betriebsmittel des Unternehmens haben.
Einbeziehung von Sicherheits- und Umweltdaten in die Analyse
Obwohl wir eine klare Vorstellung davon haben, wo wir mit den zuvor im Pareto-Diagramm sichtbaren Daten beginnen sollten, müssen wir auch den betrieblichen Kontext studieren, in dem unser Produktionssystem arbeitet. Dies liegt daran, dass unsere Grafiken nur Vermögenswerte oder Systeme enthalten, die einige Form von Ausfall erfahren haben. Es kann jedoch kritische Ausrüstung geben, die, obwohl sie zum Zeitpunkt der Untersuchung nicht versagt hat, sehr ernsthafte Konsequenzen für die körperliche Unversehrtheit der Arbeitnehmer, die Umwelt oder die globale Wirtschaft des Unternehmens haben könnte. Daher ist es notwendig, diese kritischen Vermögenswerte zu identifizieren und, wenn sie existieren, geeignete Aktionspläne für sie zu bestimmen.
Abbildung 5: Fehler nach Vermögen – Rotationssystem
In der vorherigen Grafik gibt es eine Tabelle, die eine Risikoprioritätszahl (RPN) den Vermögenswerten zuweist. Es ist wichtig, alle Systemvermögenswerte in diesen Prozess einzubeziehen, auch wenn sie schon lange nicht mehr versagt haben und nicht in unserer Analyse mithilfe von Pareto-Diagrammen erscheinen. Dies stellt sicher, dass wir keine Vermögenswerte übersehen, die die höchsten Risiken darstellen können. In diesem Artikel werden wir nicht näher auf die Verwendung der kritischen Analyse eingehen. Aber wir können nicht schließen, ohne diesen Aspekt anzuerkennen.
Techniken zur Zuverlässigkeit und Verfügbarkeit
Es gibt industrielle Zuverlässigkeitstechniken, bei denen die Verwendung von Pareto-Diagrammen und deren entsprechende Analysen ein wesentlicher Bestandteil ihrer Durchführung sind. Im Folgenden sind einige dieser Techniken mit einer kurzen Beschreibung aufgeführt:
a. Failure Mode and Effects Analysis (FMEA) Diese Technik ermöglicht es, das Risiko und die Qualität von Produkten und Prozessen mithilfe eines einzigen Werkzeugs zu bewerten. Dieses Verfahren zielt darauf ab, potenzielle Ausfälle im Prozess oder Produkt zu identifizieren und zu beschreiben, bevor sie auftreten oder an den Kunden geliefert werden. Es funktioniert sowohl für diskrete als auch für kontinuierliche Produktionsprozesse und ermöglicht die Identifizierung der Arten, in denen das System versagen kann, und ihrer entsprechenden Auswirkungen sowie des Einflusses auf die Sicherheit von Personen und die Umwelt. Die in Serviceaufträgen enthaltenen Kommentare, sowohl von Operatoren als auch von Instandhaltern, die Betriebsprobleme beschreiben und von TextAI analysiert werden, stellen sicher, dass keine Modi oder Effekte in der Analyse übersehen werden. Mit dieser Verbesserung wird die Analyse effektiver.
b. Reliability Centered Maintenance (RCM): Dies ist ein Instandhaltungskonzept, das auf der Zuverlässigkeit des Systems basiert. Ziel ist es, sicherzustellen, dass die Systeme in ihrem aktuellen Betriebskontext weiterhin wie vom Benutzer gefordert funktionieren. Eine erfolgreiche Umsetzung von RCM führt zu einer Steigerung der Rentabilität, Zuverlässigkeit und Verfügbarkeit. Es ermöglicht auch ein besseres Verständnis des Risikos, dem die Organisation ausgesetzt ist, und der Maßnahmen, die ergriffen werden können, um es zu mindern. Wenn Informationen zu Ausfällen, Prozessen und Rückmeldungen als Kommentare in ein Informationssystem aufgenommen werden, können TextAI-Tools uns dabei unterstützen, festzustellen, welche Geräte außerhalb von Instandhaltungsplänen liegen, uns auf den Zeitpunkt oder die Häufigkeit von Wartungsaktivitäten für Geräte hinweisen, die die akzeptablen Parameter überschreiten, und uns bei der Festlegung der optimalen Ausfallzeit für die Durchführung geplanter Wartungsarbeiten und der Identifizierung der benötigten Ersatzteile unterstützen.
c. Fault Tree Analysis (FTA): Dies ist eine deduktive Top-Down-Methode zur Fehleranalyse, bei der der unerwünschte Zustand eines Systems mithilfe der booleschen Logik analysiert wird, um eine Reihe von Ereignissen auf niedriger Ebene zu bestimmen. Diese Analysemethode wird hauptsächlich in den Bereichen Sicherheitstechnik und Zuverlässigkeitsengineering eingesetzt, um zu verstehen, wie Systeme versagen können, die effektivsten Möglichkeiten zur Risikoreduzierung zu identifizieren und ein erstes Verständnis der Ereignisraten innerhalb eines Systems zu erlangen. Diese Methode ist in sowohl FMEA als auch RCM-Techniken enthalten, da beide erfordern, die Hauptfunktion des Systems zu verstehen und von dort aus auf detailliertere Ebenen abzusteigen, um zu identifizieren, wie Fehlerereignisse auftreten können. Fehlermodi und -effekte können in Kommentaren von Operatoren oder Instandhaltern enthalten sein und Situationen wie den Ausfall eines Mischers aufgrund einer Überhitzung des Motors aufgrund eines Überschusses an Material in der Leitung beschreiben. Dieser Kommentar könnte darauf hinweisen, dass der Mischer seine Mischfunktion aufgrund eines Motorfehlers infolge eines Materialüberschusses verloren hat. Die von TextAI analysierte Dokumentation kann es uns ermöglichen, eine genauere Analyse durchzuführen und effektivere Maßnahmen bei der Entwicklung von Wartungsplänen zu ergreifen.
d. Root Cause Analysis (RCA): Dies ist ein strukturierter Prozess, der entwickelt wurde, um die zugrunde liegenden Ursachen eines Problems zu identifizieren. Dieser Ansatz beinhaltet das Sammeln und Analysieren relevanter Daten, um zu verstehen, warum ein Problem überhaupt aufgetreten ist. Ziel ist es, die Ursachen zu bearbeiten, um zu verhindern, dass das Problem erneut auftritt. RCA konzentriert sich statt auf oberflächliche Auswirkungen darauf, die grundlegenden Ursachen von Prozess- oder Systemausfällen zu identifizieren, wodurch es ein wertvolles Werkzeug für Problembehebung und kontinuierliche Verbesserung wird. Der erste Schritt in der Ursachenanalyse, bevor man den "5 Warum"-Ansatz verfolgt, besteht darin, das Problem und seine Ursachen zu analysieren. Nehmen wir an, die Waschmaschine macht Geräusche, und dies könnte auf Grund A oder Grund B zurückzuführen sein. Die Wartungsmaßnahme besteht darin, die Schrauben zu überprüfen und anzuziehen. Daher bedeutet dies, dass eine lockere Schraube eine mögliche Ursache ist. Software wie TextAI kann erheblich dazu beitragen, interne Ursachen anderer Systeme und/oder Fehlermodi zu analysieren, ähnlich wie im zuvor beschriebenen Beispiel. Sie kann uns bei der Durchführung der Analyse der "5 Warum" unterstützen und uns bei der Suche nach der wahren Ursache des Problems und bei der Festlegung angemessener Minderungsstrategien effektiver helfen.
Die zuvor genannten Techniken werden mit einem multidisziplinären Team umgesetzt, um vielfältige Ideen, Erfahrungen und Perspektiven einzubeziehen und ihre Wirksamkeit in der Praxis zu verbessern.
Schlussfolgerungen
In diesem Artikel haben wir gesehen, was nach der Erstellung von Pareto-Diagrammen zu tun ist und wie sie effektiv wiederkehrende Probleme angehen können, die den größten Einfluss auf verschiedene Produktions- und Fertigungssysteme haben. Wir haben gelernt, wie man eine eingehende Analyse mithilfe von Pareto-Diagrammen durchführt. Diese Analyse geht über die bloße Betrachtung der Anzahl von Ausfällen und Ausfallzeiten hinaus. Stattdessen berücksichtigen wir auch Faktoren wie Reparaturkosten und Produktionsverluste aufgrund von Stillständen. Durch die Analyse dieser verschiedenen Aspekte sind wir in der Lage, aus mehreren Perspektiven fundiertere Entscheidungen in Bezug auf die Gesamteffektivität der Anlagen (Overall Equipment Effectiveness, OEE) des Unternehmens zu treffen.
Wir verstehen, dass es nicht ausreicht, nur die in das Pareto-Diagramm aufgenommenen Anlagen zu untersuchen. Wir müssen auch eine Kritikalitätsstudie aller unserer Vermögenswerte durchführen, um solche zu identifizieren, die erhebliche Sicherheitsfolgen für Menschen haben können, Auswirkungen auf die Umwelt haben oder einen signifikanten Einfluss auf die Wirtschaft des Unternehmens haben können. All dies hängt von dem betrieblichen Kontext ab, in dem der Produktionsprozess tätig ist.
Die Verwendung von Pareto-Diagrammen mit verschiedenen Indikatoren ist ein leistungsstarkes Werkzeug, um unsere Bemühungen und Ressourcen auf Anlagen oder Prozesse auszurichten, die den größten Einfluss haben. In Kombination mit Techniken zur industriellen Zuverlässigkeit ermöglichen diese Diagramme kontinuierliche Verbesserungen, reduzieren Ausfälle und mindern Risiken. Dies wiederum steigert die Produktion und fördert die Nachhaltigkeit im Produktionsprozess.
Werkzeuge, die auf TextAI basieren, können in Lösungen integriert werden, die in jedem Stadium des Prozesses anwendbar sind. Sie haben die Fähigkeit, aus Fehlern zu lernen und Anleitung bei der Entwicklung von Analysen und Plänen zur Beseitigung von Problemen im Produktionsprozess zu geben.