HOWTO: How to Calculate Downtime Costs - Understanding the Financial Impact
See what financial impact production downtime has and how to quantify them. We show a few different costs and their formulas.
Introduction
In the relentless pursuit of operational excellence, it is critical to understand the financial consequences of downtime. According to Siemens, 2023, one hour of unplanned downtime costs the automotive industry more than $2 million, which is a 50% increase from two years ago. In this article, we will explore how to perform calculations of tangible and intangible downtime costs. We will also describe strategic concepts that can not only minimize financial losses but also improve the overall efficiency of the organization. Additionally, we will discover the fundamental role of production managers in achieving an optimized and resilient production ecosystem.
Costs of Downtime in Manufacturing
Downtime costs fall into two broad categories: tangible and intangible. Tangible costs are directly calculable expenses that are incurred during downtime, easily quantified in financial terms, and have a direct impact on the company's financial accounting. On the other hand, intangible costs are hidden and require a more in-depth analysis for calculation due to their abstract or non-physical nature. Consequently, their assessment is often more subjective and complex. The total cost of downtime comprises the sum of all tangible and intangible costs incurred during the downtime period until the production line is restored to its normal operating state.
There is no universal method to calculate downtime expenses, and the calculation, along with its associated elements, depends on the nature of the production system and the operational and market context in which the factory operates. Let's delve a bit more into the composition of these two major cost groups:
Tangible Costs
Tangible costs are associated with various factors or elements that can vary depending on the type of company. Among the tangible costs are the following:
Lost Production
The most direct cost is the lost production value. This includes the revenue you would have generated during that hour. The financial impact depends on your production rate and the value of the products you manufacture. For example, if you produce 1,000 units per hour, each generating $10 in profit, the failure affects the entire production line (100%), and the downtime lasts an hour; then an hour of downtime costs you $10,000.
Profit is defined here as revenue per piece – variable costs per piece. Be sure to include in the variable costs only those costs that you saved because of non-production (say raw materials).
The above can be summarized in the following formula:
Time of overtime
In the case of unplanned downtime, it is highly likely that personnel may need to work overtime to fix the failure. Overtime hours are generally higher than regular working hours and represent direct costs during this downtime. For example, if workers earn an average of $20/hr, and overtime has a 1.5 times regular hourly rate, the worker will receive $30/hr. If 5 workers are needed to repair the production line for 3 hours, then the total expense will be $450. The above can be summarized in the following formula:
Cost of idle labor hour
When a production line comes to a halt, workers cease working while the maintenance team addresses the issue and restores factory operations. During this time, these individuals continue to receive their salaries, even though production is halted. This expense is also considered a downtime cost or a cost resulting from reduced production. It is calculated by multiplying the number of idle hours by their average cost.
Including this cost into your total makes sense if you don't do overtime to catch up with the missed production. Otherwise you have included this aspect already there.
Example: Let's consider a production line with 20 workers earning an average of $18/hr, and a problem occurs that halts production for 3 hours. In this scenario, the company would incur $1,080 for unused labor. The above can be summarized in the following equation:
Cost of Repairs
If downtime is caused by equipment failures or technical issues, there are expenses associated with rectifying these problems and restoring normal operation. These costs will depend on the nature of our production process and may include spare parts, specialized external labor, equipment, tools, and any other resources necessary to carry out the repairs.
Missed Deadlines
Downtime can lead to missed deadlines for fulfilling customer orders. This delay may result in contractual penalties with the client, which, if applicable, are direct expenses associated with the downtime. The cost of this will depend on what is specified in the contract.
Intangible Costs
Intangible costs, such as reputation damage, can have a significant impact on your business. Downtime can lead to a loss of customer trust, missed deadlines, and potential customer loss. While it may be difficult to precisely quantify these costs, having an understanding of their potential long-term impact can help you recognize the value of investing in a business continuity plan.
Loss of Customer Trust
If a plant shutdown ends up delaying product delivery to a customer, this impacts our customer's trust in the commitments and promises we made to them. This lack of trust can affect the company in the long run as it creates dissatisfied customers, potential customer loss, and damage to the organization's reputation.
There is no precise formula to calculate these costs as it involves subjective elements. However, conducting customer satisfaction surveys, monitoring customer retention rates, and assessing the public perception of our organization can provide key indicators to estimate this intangible cost.
Operational Disruption
In the realm of manufacturing, operational disruption costs refer to the negative effects on internal organizational operations caused by unplanned interruptions in productive activities. Picture this: a factory experiences an unscheduled halt due to a critical machinery breakdown. Throughout this period, operational disruption may manifest itself in several ways.
Production Delays: Assembly lines grind to a halt, leading to the accumulation of unfinished products. Work Inefficiencies: Restricted access to specific plant areas can hamper employee efficiency. Need for Reorganization: Management must reshuffle tasks and allocate resources to address the unforeseen stoppage.
Given the multifaceted qualitative nature of operational disruption, there is no standardized formula for calculating it. However, keeping a close eye on lost work hours, operational efficiency, and the necessity for planning adjustments can serve as indicators, offering insights into the extent of this disruption.
Costs in OEE Percentage points
For companies using OEE it's often handy to use OEE-percentage losses as basis for your cost estimation.
These costs reflect the loss of efficiency in operational performance due to an unplanned shutdown. Let's use an example to better understand this concept.
Let's consider a manufacturing facility with a target OEE of 85%. During a specific unplanned downtime event, the actual OEE drops to 70%. The scheduled production for that period was 1,000 units.
OEE Percentage Point Costs = (Target OEE-Actual OEE) × Scheduled Production
OEE Percentage Point Costs = (85%−70%) × 1,000
OEE Percentage Point Costs = 150 units
The calculation shows that during this unplanned downtime, the facility incurred OEE Percentage Point Costs of 150 units. This means the operation fell short by 15 percentage points from its target efficiency. The cost reflects the impact on scheduled production, which could result in reduced output, increased waste, or a decline in final product quality.
Let's approach the above from a different perspective. What is the economic value of 1 point of my OEE? Suppose we currently have an OEE percentage in our factory of 70%, a daily production of 1,000 units, and a profit per unit of $20, using the following formula:
Dollar Value per OEE Percentage Point = Pieces per Percentage Point × Profit per Piece
Pieces per Percentage Point = ((Output per Day)/(Current OEE))
Pieces per Percentage Point = ((1,000 piece/day)/70) = 14.28 pieces per %OEE point per day
Now, let's calculate the economic impact:
Dollar Value per OEE Percentage Point = 14.28 × profit per piece
Dollar Value per OEE Percentage Point = (14.28) × 20 $/piece
Dollar Value per OEE Percentage Point = 285.71 $/day
Dollar Value per OEE Percentage Point = 105k $/year
So, if you increase the OEE by 1 point, you gain an additional $285.60 per day. Extrapolating this to a yearly scale, you would gain $105k/year.
Keeping the value of 1 percentage point in mind, helps you justify improvements/investments in your operation.
Showcasing the Financial Impact of Downtime Reduction
The financial landscape of manufacturing is under siege as unplanned downtime exacts a toll more severe than ever before, a revelation exposed by Siemens in their 2023 report, "The True Cost of Downtime 2022" The staggering numbers and examples presented in this report paint a vivid picture of the financial havoc wreaked by downtime, emphasizing the imperative for businesses to take decisive action.
Siemens' report discloses that the cost of an hour of unplanned downtime has skyrocketed, escalating by at least 50% across every sector surveyed compared to two years ago. The automotive industry, for instance, now faces a staggering cost of over $2 million per hour, a substantial leap from $1.3 million in the previous survey. In the Oil & Gas sector, the cost has more than doubled in just two years, reaching nearly $500,000 per hour.
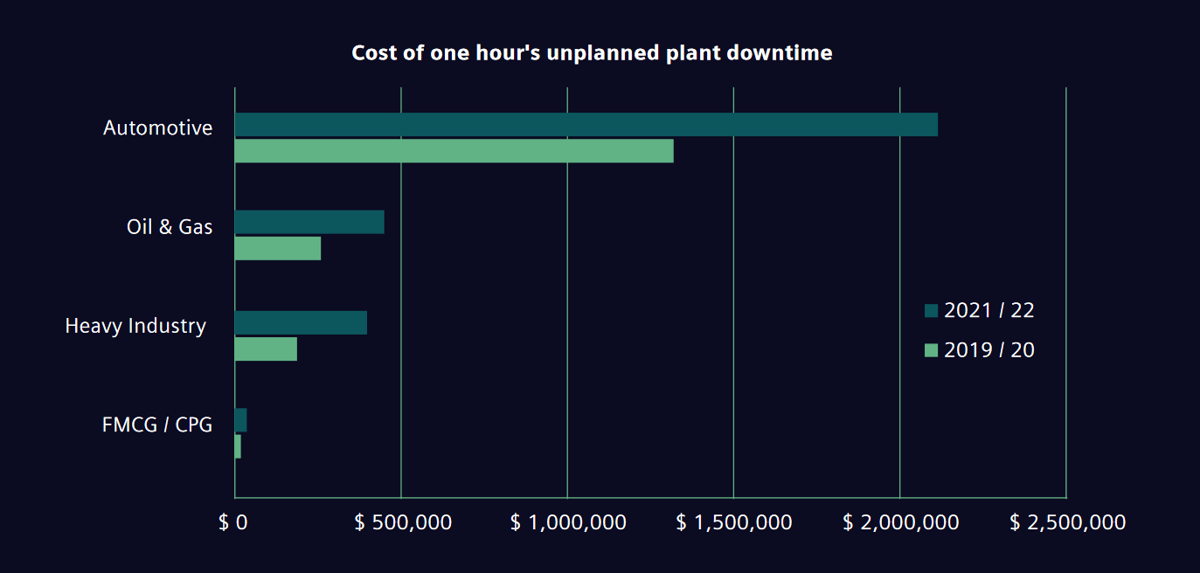
Figure 1: Cost of one hour's unplanned plant downtime. (Siemens, 2023)
Total losses due to downtime are on a sharp ascent, with an estimated cost of $129 million per year for an average large plant, marking a 65% increase in just two years. Fortune Global 500 industrial organizations collectively hemorrhage almost $1.5 trillion annually due to unplanned downtime, constituting 11% of their turnover.
This financial onslaught, however, has been mitigated by firms leveraging Predictive Maintenance strategies and Industry 4.0 technologies, resulting in a reduction in the number of unplanned downtime incidents. The average manufacturing facility, for example, experiences six fewer downtime incidents per month compared to two years ago. Yet, an average large plant still loses 25 hours per month to unplanned downtime.
A full-scale adoption of condition monitoring and predictive maintenance practices at Fortune Global 500 industrial organizations could yield an annual saving of 1.6 million hours of downtime, translating to a substantial $734 billion increase in productivity and a $236 billion reduction in maintenance costs. Collecting pertinent data emerges as a pivotal factor in enabling Predictive Maintenance. While more than three-quarters of businesses collect basic data, the most successful ones go beyond, integrating IoT platforms to harness data from multiple sources. This approach enhances machine learning and AI predictions, providing a more nuanced understanding of equipment health.
The financial impact of downtime reduction is not only about saving substantial sums but also about improving overall efficiency, sustainability, and resilience. Predictive Maintenance, powered by AI-driven machine-health monitoring, emerges as a beacon of financial salvation for manufacturers, offering not just economic gains but also fostering a greener and more sustainable industrial landscape.
Maximizing Efficiency for Downtime Reduction
As a Production Manager
In the tireless pursuit of minimizing downtime, production managers are architects of efficient operations. By strategically implementing different maintenance methodologies and leveraging real-time data, production managers can address equipment issues in a variety of ways, dramatically reducing unplanned downtime. One of their key roles is to develop robust maintenance programs, adopt innovative technologies, and foster a proactive culture among the production team. Through close supervision and responsive decision-making, production managers not only optimize operational efficiency but also strengthen the company's bottom line.
Leveraging Managerial Efforts for a Multiplication Effect
Management efforts serve as a multiplier effect in reducing downtime. In this task, managers must manage to reduce the number of unscheduled stops as well as the reduction of downtime associated with both scheduled and unscheduled stops. By aligning teams with a shared vision, managers create a culture of proactive problem solving. Managerial foresight in optimizing workflows and adopting innovative solutions ripples through the organizational fabric, fostering a greater state of efficiency. Through strategic planning and decisive actions, managers drive a ripple effect, minimizing downtime and amplifying overall operational productivity.
Removing Blockers for Enhanced Efficiency
In the pursuit of operational excellence, identifying and eliminating blockers becomes paramount for downtime reduction. A production environment free from impediments allows seamless workflow and quick issue resolution. By conducting thorough analyses of processes, production managers can proactively identify potential bottlenecks and devise strategic solutions. Whether it's streamlining communication channels or investing in cutting-edge technologies, the removal of blockers catalyzes heightened efficiency. Embracing a culture of continuous improvement further ensures a dynamic and resilient production ecosystem. As the barriers diminish, the path to downtime reduction becomes clearer, unleashing the full potential of streamlined operations and enhanced productivity.
Conclusion
In the intricate landscape of manufacturing, decoding downtime costs is pivotal for financial resilience. As revealed by Siemens' 2023 report, the financial impact of unplanned downtime has surged, with the automotive industry grappling with a staggering $2 million per hour cost. This financial onslaught, however, finds its antidote in predictive maintenance and Industry 4.0 technologies, offering a potential annual saving of 1.6 million hours of downtime and a monumental boost of $734 billion in productivity. This article explores the significance of determining downtime costs, providing a roadmap for calculating tangible and intangible expenses. For production managers, the key lies in strategic maintenance, real-time data utilization, and fostering a proactive ethos among teams. Managerial efforts, when aligned with a shared vision, act as a multiplier in minimizing downtime, while the removal of blockers ensures a path of streamlined operations and heightened productivity. Embracing these insights not only safeguards against financial losses but also propels manufacturers toward a greener and more sustainable industrial future.