HOWTO: Wie man Ausfallkosten berechnet - Verständnis für die finanziellen Auswirkungen
Erfahre, welche finanziellen Auswirkungen Produktionsausfallzeiten haben und wie man sie quantifiziert. Wir zeigen einige verschiedene Kosten und ihre Formeln.
Einführung
Im unerbittlichen Streben nach betrieblicher Exzellenz ist es entscheidend, die finanziellen Folgen von Ausfallzeiten zu verstehen. Laut Siemens, 2023, kostet eine Stunde ungeplanter Stillstand die Automobilindustrie mehr als 2 Millionen Dollar, was einem Anstieg von 50 % in den letzten zwei Jahren entspricht. In diesem Artikel werden wir erkunden, wie man Berechnungen der greifbaren und immateriellen Ausfallkosten durchführt. Wir werden auch strategische Konzepte beschreiben, die nicht nur finanzielle Verluste minimieren, sondern auch die Gesamteffizienz der Organisation verbessern können. Darüber hinaus werden wir die grundlegende Rolle von Produktionsmanagern bei der Erreichung eines optimierten und widerstandsfähigen Produktionsökosystems entdecken.
Kosten von Ausfallzeiten in der Fertigung
Ausfallkosten fallen in zwei Hauptkategorien: greifbare und immaterielle Kosten. Greifbare Kosten sind direkt berechenbare Ausgaben, die während der Ausfallzeit anfallen, leicht in finanziellen Begriffen quantifizierbar sind und einen direkten Einfluss auf die finanzielle Buchführung des Unternehmens haben. Im Gegensatz dazu sind immaterielle Kosten verborgen und erfordern aufgrund ihrer abstrakten oder nicht-physischen Natur eine tiefere Analyse für die Berechnung. Folglich ist ihre Bewertung oft subjektiver und komplexer. Die Gesamtkosten von Ausfallzeiten umfassen die Summe aller greifbaren und immateriellen Kosten, die während des Ausfallzeitraums bis zur Wiederherstellung der Produktionslinie in ihren normalen Betriebszustand entstehen.
Es gibt keine universelle Methode zur Berechnung von Ausfallkosten, und die Berechnung sowie die zugehörigen Elemente hängen von der Natur des Produktionssystems und dem betrieblichen sowie marktlichen Kontext ab, in dem die Fabrik tätig ist. Lassen Sie uns etwas genauer auf die Zusammensetzung dieser beiden Hauptkostengruppen eingehen:
Greifbare Kosten
Greifbare Kosten sind mit verschiedenen Faktoren oder Elementen verbunden, die je nach Art des Unternehmens variieren können. Zu den greifbaren Kosten gehören unter anderem:
Verlorene Produktion
Die direkteste Kosten sind der Wert der verlorenen Produktion. Dies umfasst den Umsatz, den du während dieser Stunde generiert hättest. Die finanzielle Auswirkung hängt von deiner Produktionsrate und dem Wert der von dir hergestellten Produkte ab. Wenn du zum Beispiel 1.000 Einheiten pro Stunde produzierst, die jeweils 10 $ Gewinn generieren, und der Ausfall die gesamte Produktionslinie (100 %) betrifft und die Ausfallzeit eine Stunde dauert, dann kostet dich eine Stunde Ausfallzeit 10.000 $.
Gewinn wird hier definiert als Umsatz pro Stück - variable Kosten pro Stück. Achte darauf, in den variablen Kosten nur die Kosten einzubeziehen, die du aufgrund der Nichtproduktion eingespart hast (zum Beispiel Rohstoffe).
Das oben Gesagte lässt sich in folgender Formel zusammenfassen:
Überstundenkosten
Im Falle ungeplanter Ausfallzeiten ist es sehr wahrscheinlich, dass Personal Überstunden arbeiten muss, um die Störung zu beheben. Überstundenstunden sind in der Regel höher als die normalen Arbeitsstunden und stellen direkte Kosten während dieser Ausfallzeit dar. Wenn zum Beispiel Arbeiter durchschnittlich 20 $/Std. verdienen und Überstunden den 1,5-fachen regulären Stundensatz haben, erhält der Arbeiter 30 $/Std. Wenn 5 Arbeiter benötigt werden, um die Produktionslinie für 3 Stunden zu reparieren, belaufen sich die Gesamtkosten auf 450 $. Das oben Gesagte lässt sich in folgender Formel zusammenfassen:
Kosten der Leerlaufarbeitsstunde
Wenn eine Produktionslinie zum Stillstand kommt, arbeiten die Arbeiter nicht, während das Instandhaltungsteam das Problem behebt und den Fabrikbetrieb wiederherstellt. Während dieser Zeit erhalten diese Personen weiterhin ihre Gehälter, obwohl die Produktion gestoppt ist. Diese Ausgabe wird ebenfalls als Ausfallzeitkosten oder Kosten aufgrund reduzierter Produktion betrachtet. Sie wird berechnet, indem die Anzahl der Leerlaufstunden mit den durchschnittlichen Kosten multipliziert wird.
Es macht Sinn, diese Kosten in deine Gesamtkosten einzubeziehen, wenn du keine Überstunden machst, um die verpasste Produktion nachzuholen. Andernfalls hast du diesen Aspekt bereits dort eingeschlossen.
Beispiel: Betrachten wir eine Produktionslinie mit 20 Arbeitern, die im Durchschnitt 18 $/Std. verdienen, und es tritt ein Problem auf, das die Produktion für 3 Stunden stoppt. In diesem Szenario würde das Unternehmen 1.080 $ für ungenutzte Arbeitskraft anfallen. Das oben Gesagte lässt sich in folgender Gleichung zusammenfassen:
Reparaturkosten
Wenn Ausfallzeiten durch Geräteausfälle oder technische Probleme verursacht werden, entstehen Kosten für die Behebung dieser Probleme und die
Wiederherstellung des normalen Betriebs. Diese Kosten hängen von der Natur unseres Produktionsprozesses ab und können Ersatzteile, spezialisierte externe Arbeitskräfte, Ausrüstung, Werkzeuge und alle anderen Ressourcen umfassen, die für die Reparaturen erforderlich sind.
Verpasste Fristen
Ausfallzeiten können zu verpassten Fristen bei der Erfüllung von Kundenaufträgen führen. Diese Verzögerung kann zu Vertragsstrafen mit dem Kunden führen, die, falls zutreffend, direkte Ausgaben im Zusammenhang mit der Ausfallzeit sind. Die Kosten dafür hängen davon ab, was im Vertrag festgelegt ist.
Immaterielle Kosten
Immaterielle Kosten wie Reputationsschäden können einen erheblichen Einfluss auf dein Geschäft haben. Ausfallzeiten können zu einem Verlust des Kundenvertrauens, verpassten Fristen und potenziellem Kundenverlust führen. Obwohl es schwierig sein kann, diese Kosten genau zu quantifizieren, kann das Verständnis ihres potenziellen langfristigen Einflusses dir helfen, den Wert einer Investition in einen Geschäftskontinuitätsplan zu erkennen.
Verlust des Kundenvertrauens
Wenn ein Stillstand der Anlage zu einer Verzögerung der Produktlieferung an einen Kunden führt, beeinflusst dies das Vertrauen unseres Kunden in die Zusagen und Versprechen, die wir ihm gemacht haben. Dieses fehlende Vertrauen kann das Unternehmen langfristig beeinträchtigen, da es unzufriedene Kunden, potenziellen Kundenverlust und Schäden am Ruf der Organisation verursacht.
Es gibt keine genaue Formel zur Berechnung dieser Kosten, da subjektive Elemente eine Rolle spielen. Es können jedoch Kundenzufriedenheitsumfragen durchgeführt, Kundenbindungsquoten überwacht und die öffentliche Wahrnehmung unserer Organisation bewertet werden, um wichtige Indikatoren für die Schätzung dieser immateriellen Kosten zu erhalten.
Betriebsstörungen
Im Bereich der Fertigung beziehen sich Kosten für Betriebsstörungen auf die negativen Auswirkungen auf die internen betrieblichen Abläufe, die durch ungeplante Unterbrechungen in produktiven Aktivitäten verursacht werden. Stelle dir vor: Eine Fabrik erlebt einen ungeplanten Stillstand aufgrund eines kritischen Maschinenausfalls. Während dieses Zeitraums kann sich eine Betriebsstörung auf verschiedene Arten manifestieren.
Produktionsverzögerungen: Montagelinien kommen zum Stillstand, was zu einer Ansammlung von unfertigen Produkten führt. Arbeitsineffizienzen: Beschränkter Zugang zu bestimmten Bereichen der Anlage kann die Effizienz der Mitarbeiter beeinträchtigen. Bedarf an Neuanordnung: Die Geschäftsleitung muss Aufgaben neu verteilen und Ressourcen zuweisen, um die unvorhergesehene Stilllegung zu bewältigen.
Angesichts der facettenreichen qualitativen Natur von Betriebsstörungen gibt es keine standardisierte Formel für die Berechnung. Das genaue Beobachten von verlorenen Arbeitsstunden, betrieblicher Effizienz und der Notwendigkeit von Plananpassungen kann jedoch als Indikator dienen und Einblicke in das Ausmaß dieser Störung bieten.
Kosten in OEE-Prozentsätzen
Für Unternehmen, die OEE verwenden, ist es oft praktisch, OEE-Prozentverluste als Grundlage für deine Kostenschätzung zu verwenden.
Diese Kosten spiegeln den Verlust an Effizienz in der betrieblichen Leistung aufgrund eines ungeplanten Stillstands wider. Lassen uns ein Beispiel verwenden, um dieses Konzept besser zu verstehen.
Nehmen wir eine Produktionsanlage mit einem Ziel-OEE von 85 % an. Während eines bestimmten ungeplanten Stillstandsereignisses sinkt der tatsächliche OEE auf 70 %. Die geplante Produktion für diesen Zeitraum betrug 1.000 Einheiten.
OEE-Prozentsatzpunkt-Kosten = (Ziel-OEE - Tatsächlicher OEE) × Geplante Produktion
OEE-Prozentsatzpunkt-Kosten = (85 % - 70 %) × 1.000
OEE-Prozentsatzpunkt-Kosten = 150 Einheiten
Die Berechnung zeigt, dass während dieses ungeplanten Stillstands die Anlage OEE-Prozentsatzpunkt-Kosten von 150 Einheiten hatte. Das bedeutet, dass die Betriebsleistung um 15 Prozentpunkte unter ihrer Ziel-Effizienz lag. Die Kosten spiegeln die Auswirkungen auf die geplante Produktion wider, was zu reduziertem Output, erhöhtem Abfall oder einem Rückgang der Endproduktqualität führen kann.
Lassen uns dies aus einer anderen Perspektive betrachten. Was ist der wirtschaftliche Wert von 1 Punkt meines OEE? Angenommen, wir haben derzeit einen OEE-Prozentsatz in unserer Fabrik von 70 %, eine tägliche Produktion von 1.000 Einheiten und einen Gewinn pro Einheit von 20 $. Dies lässt sich mit der folgenden Formel berechnen:
Dollarwert pro OEE-Prozentsatzpunkt = Stücke pro Prozentsatzpunkt × Gewinn pro Stück
Stücke pro Prozentsatzpunkt = ((Ausstoß pro Tag)/(Aktueller OEE))
Stücke pro Prozentsatzpunkt = ((1.000 Stück/Tag)/70) = 14,28 Stücke pro %OEE-Punkt pro Tag
Nun berechnen wir den wirtschaftlichen Einfluss:
Dollarwert pro OEE-Prozentsatzpunkt = 14,28 × Gewinn pro Stück
Dollarwert pro OEE-Prozentsatzpunkt = (14,28) × 20 $/Stück
Dollarwert pro OEE-Prozentsatzpunkt = 285,71 $/Tag
Dollarwert pro OEE-Prozentsatzpunkt = 105.000 $/Jahr
Wenn du den OEE um 1 Punkt steigerst, erhältst du zusätzlich 285,60 $ pro Tag. Hochgerechnet auf eine jährliche Skala würde dies einen Gewinn von 105.000 $/Jahr bedeuten.
Die Berücksichtigung des Werts von 1 Prozentpunkt hilft dir, Verbesserungen/Investitionen in deinem Betrieb zu rechtfertigen.
Darstellung der finanziellen Auswirkungen der Reduzierung von Ausfallzeiten
Die finanzielle Landschaft der Fertigung steht unter Beschuss, da ungeplante Ausfallzeiten eine noch nie dagewesene Belastung verursachen, eine Enthüllung, die Siemens in ihrem Bericht von 2023, "The True Cost of Downtime 2022", offenbart hat. Die beeindruckenden Zahlen und Beispiele in diesem Bericht zeichnen ein lebhaftes Bild der finanziellen Verwüstung, die durch Ausfallzeiten verursacht wird, und betonen die Notwendigkeit für Unternehmen, entschlossen zu handeln.
Der Bericht von Siemens enthüllt, dass die Kosten einer Stunde ungeplanter Ausfallzeit in jedem untersuchten Sektor um mindestens 50 % gegenüber vor zwei Jahren gestiegen sind. Die Automobilindustrie sieht sich beispielsweise nun mit enormen Kosten von über 2 Millionen Dollar pro Stunde konfrontiert, ein erheblicher Anstieg von 1,3 Millionen Dollar in der vorherigen Umfrage. Im Bereich Öl & Gas hat sich der Kostenbetrag in nur zwei Jahren mehr als verdoppelt und liegt nun bei fast 500.000 Dollar pro Stunde.
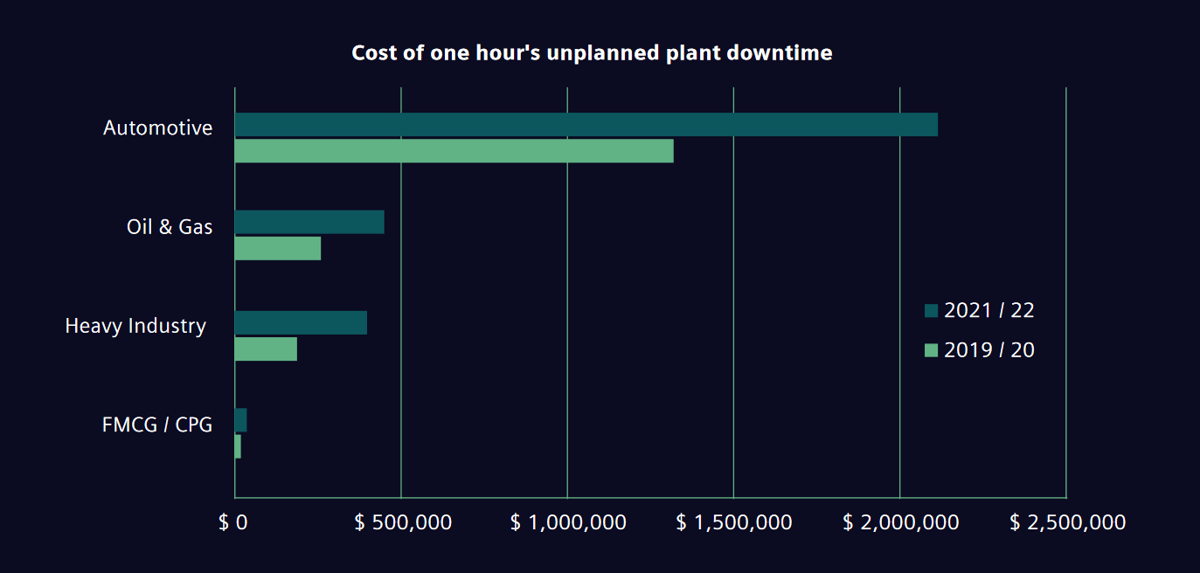
Abbildung 1: Kosten einer Stunde ungeplanter Anlagenstillstand. (Siemens, 2023)
Die Gesamtverluste aufgrund von Ausfallzeiten nehmen steil zu, mit geschätzten Kosten von 129 Millionen Dollar pro Jahr für eine durchschnittlich große An
lage, was einem Anstieg von 65 % in nur zwei Jahren entspricht. Fortune Global 500 Industrieunternehmen verlieren jährlich fast 1,5 Billionen Dollar aufgrund ungeplanter Ausfallzeiten, was 11 % ihres Umsatzes ausmacht.
Diese finanzielle Belastung wurde jedoch durch Unternehmen gemildert, die auf vorbeugende Wartungsstrategien und Technologien der Industrie 4.0 setzen, was zu einer Verringerung der Anzahl von ungeplanten Ausfallzeitvorfällen führt. Die durchschnittliche Fertigungsanlage verzeichnet beispielsweise sechs weniger Ausfallzeitvorfälle pro Monat im Vergleich zu vor zwei Jahren. Dennoch verliert eine durchschnittlich große Anlage immer noch 25 Stunden pro Monat aufgrund ungeplanter Ausfallzeiten.
Eine flächendeckende Einführung von Zustandsüberwachung und vorbeugenden Wartungspraktiken bei Fortune Global 500 Industrieunternehmen könnte zu einer jährlichen Einsparung von 1,6 Millionen Stunden Ausfallzeit führen, was zu einem erheblichen Anstieg von 734 Milliarden Dollar in der Produktivität und einer Reduzierung der Wartungskosten um 236 Milliarden Dollar führt.
Die Sammlung relevanter Daten erweist sich als entscheidender Faktor, um vorbeugende Wartung zu ermöglichen. Während mehr als drei Viertel der Unternehmen grundlegende Daten sammeln, gehen die erfolgreichsten über diese hinaus und integrieren IoT-Plattformen, um Daten aus mehreren Quellen zu nutzen. Dieser Ansatz verbessert maschinelles Lernen und KI-Vorhersagen und bietet ein nuancierteres Verständnis der Maschinengesundheit.
Die finanziellen Auswirkungen der Reduzierung von Ausfallzeiten beziehen sich nicht nur auf die Einsparung erheblicher Summen, sondern auch auf die Verbesserung der Gesamteffizienz, Nachhaltigkeit und Widerstandsfähigkeit. Die vorhersagende Wartung, unterstützt durch KI-gesteuerte Überwachung der Maschinengesundheit, erweist sich als ein Leuchtfeuer der finanziellen Rettung für Hersteller, das nicht nur wirtschaftliche Gewinne bietet, sondern auch eine grünere und nachhaltigere industrielle Landschaft fördert.
Maximierung der Effizienz zur Reduzierung von Ausfallzeiten
Als Produktionsleiter
In der unermüdlichen Suche nach Minimierung von Ausfallzeiten sind Produktionsleiter Architekten effizienter Betriebsabläufe. Durch die strategische Umsetzung verschiedener Instandhaltungsmethoden und die Nutzung von Echtzeitdaten können Produktionsleiter Ausrüstungsprobleme auf verschiedene Weisen angehen und ungeplante Ausfallzeiten dramatisch reduzieren. Eine ihrer Schlüsselrollen besteht darin, robuste Instandhaltungsprogramme zu entwickeln, innovative Technologien zu übernehmen und eine proaktive Kultur im Produktionsteam zu fördern. Durch enge Überwachung und reaktionsschnelles Entscheiden optimieren Produktionsleiter nicht nur die betriebliche Effizienz, sondern stärken auch die finanzielle Gesundheit des Unternehmens.
Hebeln von Managementbemühungen für einen Multiplikatoreffekt
Managementbemühungen wirken sich als Multiplikatoreffekt bei der Reduzierung von Ausfallzeiten aus. In dieser Aufgabe müssen Manager die Anzahl ungeplanter Stillstände ebenso reduzieren wie die Verringerung von Ausfallzeiten, die mit sowohl geplanten als auch ungeplanten Stillständen verbunden sind. Indem sie Teams mit einer gemeinsamen Vision ausrichten, schaffen Manager eine Kultur proaktiver Problemlösung. Managerielle Voraussicht bei der Optimierung von Arbeitsabläufen und der Einführung innovativer Lösungen zieht sich durch das organisatorische Gefüge und fördert einen höheren Effizienzzustand. Durch strategische Planung und entschlossenes Handeln erzeugen Manager einen Ripple-Effekt, der Ausfallzeiten minimiert und die gesamte betriebliche Produktivität verstärkt.
Beseitigung von Hindernissen für eine gesteigerte Effizienz
Auf dem Weg zur operativen Exzellenz wird die Identifizierung und Beseitigung von Hindernissen für die Reduzierung von Ausfallzeiten entscheidend. Eine Produktionsumgebung ohne Behinderungen ermöglicht einen nahtlosen Workflow und eine schnelle Problemlösung. Durch gründliche Analysen von Prozessen können Produktionsleiter potenzielle Engpässe proaktiv identifizieren und strategische Lösungen entwickeln. Ob durch Optimierung von Kommunikationskanälen oder Investitionen in modernste Technologien, die Beseitigung von Hindernissen katalysiert eine gesteigerte Effizienz. Die Annahme einer Kultur kontinuierlicher Verbesserung gewährleistet außerdem ein dynamisches und widerstandsfähiges Produktionsumfeld. Mit dem Verschwinden der Barrieren wird der Weg zur Reduzierung von Ausfallzeiten klarer, und das volle Potenzial von effizienten Abläufen und gesteigerter Produktivität entfaltet sich.
Schlussfolgerung
In der komplexen Welt der Fertigung ist das Dekodieren der Ausfallzeiten von entscheidender Bedeutung für finanzielle Resilienz. Wie im Bericht von Siemens für 2023 offenbart, hat der finanzielle Einfluss ungeplanter Ausfallzeiten zugenommen, und die Automobilindustrie sieht sich mit enormen Kosten von 2 Millionen Dollar pro Stunde konfrontiert. Dieser finanzielle Angriff findet jedoch seine Antwort in vorhersagender Wartung und Technologien der Industrie 4.0, die eine potenzielle jährliche Einsparung von 1,6 Millionen Stunden Ausfallzeit und einen monumentalen Anstieg von 734 Milliarden Dollar in der Produktivität bieten.
Dieser Artikel untersucht die Bedeutung der Bestimmung von Ausfallzeiten und bietet eine Roadmap zur Berechnung von greifbaren und immateriellen Kosten. Für Produktionsmanager liegt der Schlüssel in strategischer Wartung, der Nutzung von Echtzeitdaten und der Förderung einer proaktiven Haltung in den Teams. Manageriale Bemühungen, wenn sie mit einer gemeinsamen Vision abgestimmt sind, wirken als Multiplikator zur Minimierung von Ausfallzeiten, während die Beseitigung von Hindernissen einen Weg zu effizienten Abläufen und gesteigerter Produktivität sicherstellt. Die Umsetzung dieser Erkenntnisse schützt nicht nur vor finanziellen Verlusten, sondern treibt die Hersteller auch in Richtung einer grüneren und nachhaltigeren industriellen Zukunft.